Our technology
CRYSTTAL is an acryonym for CRYogenic Suspension for TreaTment And Loading; it is a new nano/micronization nano/micronization technology. Eight years of research were necessary to develop the CRYSTTAL process. It represents a breakthrough in the material grinding sector.
The CRYSTTAL technology is based on the direct cryo-micronization of materials. It is the only technology that can achieve submicron and nanometric grinding of all materials, even ductile, reactive, or heat-sensitive materials. The process is 10 times faster than reference processes and enables granulometry to be finely controlled. CRYSTTAL opens up new horizons in terms of properties (bio-assimilation, catalysis, electromagnetic performance, etc.) and therefore new markets.
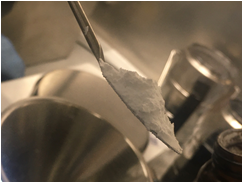
CRYSTTAL opens up new horizons in terms of properties (bio-assimilation, catalysis, electromagnetic performance….) and therefore new markets.
An innovative process and high-performance technology
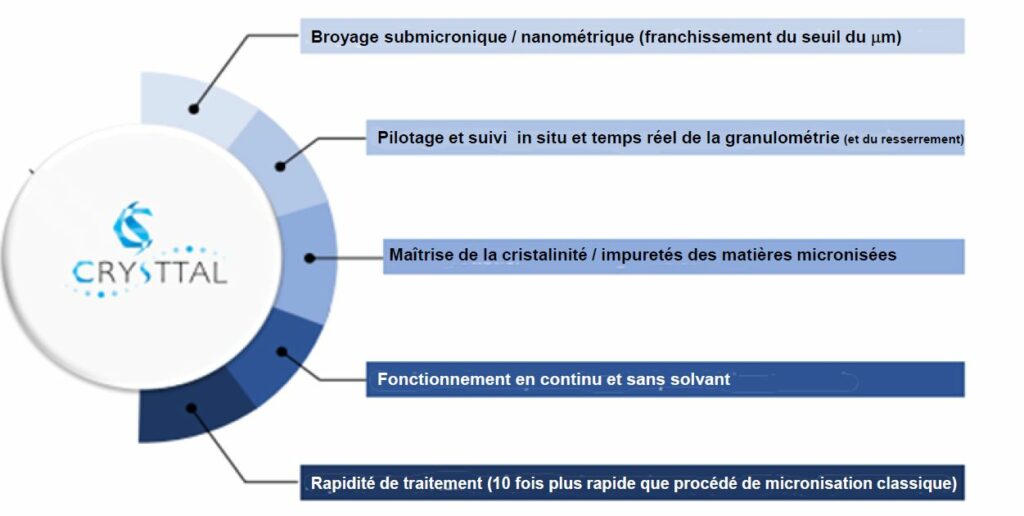
Technology with high added-value
- Mixtures are more homogeneous , even mixtures of cohesive powders
- Powder oxidation reduced
- Powder purity is maintained : no pollution, no structural transformation, no reaction
- Initial physical and chemical properties of micronized materials are preserved
- Performance properties of use are improved
- Very high grinding efficiency: 95% of the material is recovered in powder form
Clean technology
- Does not produce effluents
- Does not produce dust or aerosols
- Does not consume water, solvents or chemical additives
- Low power consumption due to reduced grinding time
Why ?
CRYSTTAL fills a technological gap and
opens up a wide range of new applications.
All materials
The CRYSTTAL technology can grind a wide range of ductile, reactive (oxidizable, soluble, heat-sensitive, etc.) and dangerous (toxic or explosive) materials, which until now could not be ground to a fine powder state with the available technologies.
Almost 70% of processed goods across all sectors are manufactured from powders: pharmaceuticals, cosmetics, food, etc. Micronization is a key stage in most manufacturing processes. This complex operation calls into play many phenomena and involves numerous parameters that need adjusting to gain fine control of the materials being micronized. It has been the subject of major R&D programs.
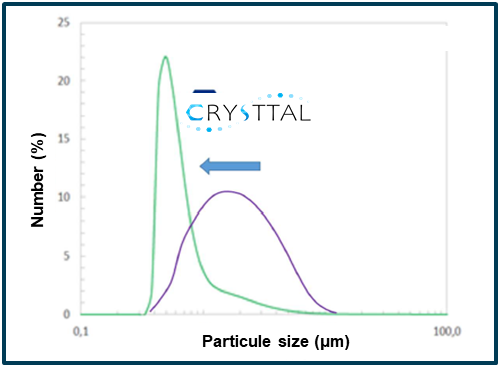
Comparison of particle size distribution obtained by the
CRYSTTAL process and conventional grinding.
Adapted to industrial constraints
Presented for the first time at the 12th Rencontres CEA-Industrie in 2019, the CRYSTTAL technology has attracted industry partners from many sectors because it removes technical barriers to the development of new, high value-added powders required by many markets, and it capable of producing unusual powders at production costs compatible with industrial constraints.
With traditional technologies, it is very difficult and costly to produce industrial-scale powders of sizes between 10 nm and 1 mm. Yet the submicron scale improves the functional properties of materials: better thermomechanical, optical, electrical, electromagnetic, and solubility/bio-assimilation behavior, etc. CRYSTTAL is the only technology that allows direct, in situ control of the powder granulometry during the micronizing step.